Fast Turn-around
MVP Green Belt Training Aids Cycle Times at Morrey Nissan
January 29 2020, Morrey Auto Body and Glass
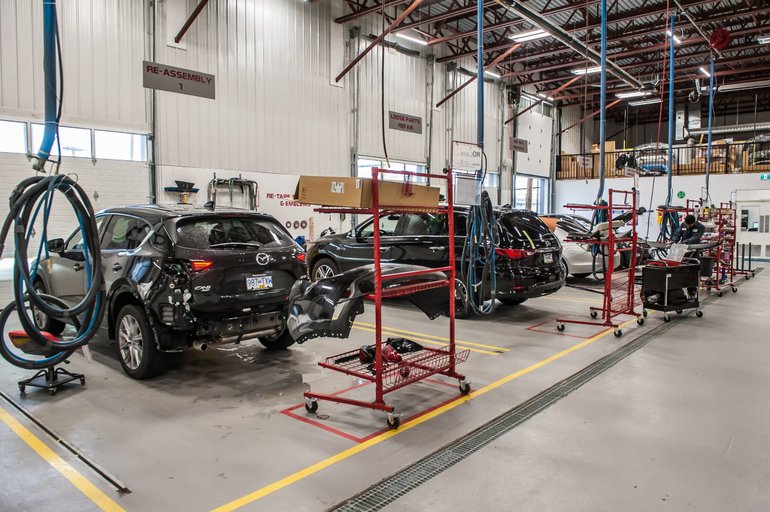
Same-day delivery. On-demand entertainment. Instant meals. Everywhere you look, consumers are demanding that things happen more quickly—and auto body repair is no exception. Recently, a $10,000 repair on a Nissan Rogue was completed in a single day at the Morrey Auto Body Shop in Burnaby, British Columbia. How? New ways of thinking, new processes and a new facility built around Lean Six Sigma knowledge gained from PPG MVP Green Belt Training.
“Green Belt Training is an eye-opener,” says Michael Leyland, manager of the collision center for four Morrey Auto Group dealerships located in metro Vancouver. “I am excited to see how far we can take it. If we had treated that Rogue like we would have before, it would have been at our facility for a week or more, possibly longer if we had run into a backorder on parts.”
With Lean Six Sigma, incremental changes lead to big results. At Morrey Auto Body Shop, those small changes are primarily focused around one objective: eliminating delays through X-RAY REPAIR PLANNING.®
In the case of the Nissan Rogue, the damage was to the front and back bumper and tailgate–but the car was still drivable. The customer came in for consultation, a repair plan was mapped out, and he was able to leave in his own vehicle. In the meantime, new parts (front bumper, rear bumper and tailgate) were ordered and when they came in, were repainted to match the vehicle. When the customer returned a few days later, he was loaned a Nissan Leaf electric car for the day, the parts were swapped out, and his original vehicle was ready to go.
Turnaround like that isn’t always possible, but when it is, it’s a pleasant surprise for the vehicle owner.
“A big part of what we do is education,” explains Leyland. “It can be challenging to ask a customer to come to our facility on two separate occasions when they are used to just showing up and leaving with a rental car. We have to educate them about the benefit of their vehicle not being out of service for an extended period.”
Careful repair planning also results in reduced frustration and downtime for technicians. “Teaching them that this process was created to help them be more productive is important for their buy-in into the process. Now, the techs can be touching the car from start to finish without any delays.” To avoid any delays, the Morrey collision repair team conducts a checkpoint two days prior to the scheduled repair. At this juncture, they verify that all parts have been received, are correct, and are not damaged—“down to the last clip,” says Leyland.
The collision center was able to more fully implement the practical application of Lean Six Sigma in 2017 when they built an all-new facility, going from 9,000 to 14,000 square feet of dedicated space. Workflow was optimized with assistance from PPG’s MVP Layout & Design team. Their local FinishMaster distributor was instrumental in helping to get the new facility up and running, and recently helped the company implement a new material management system, which will also work to avoid delays.
Leyland points to sales as the ultimate proof that the journey into Lean Six Sigma processes has been worthwhile. Capped out at $275–300K in the old facility, the new facility is already producing at a pace of $350–$400K per month. “That is 100% because of the processes we’ve implemented to eliminate delays,” says Michael.